Кракен действующая ссылка
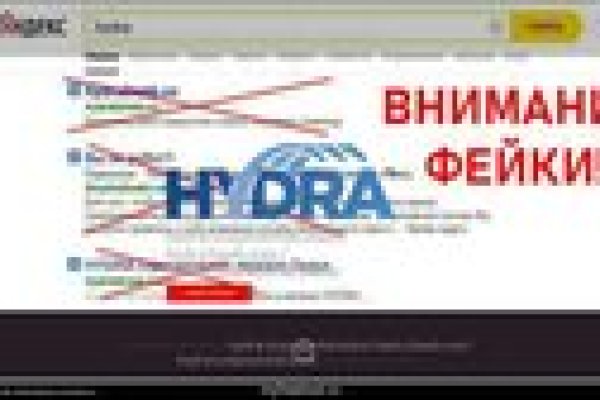
Onion - The Pirate Bay,.onion зеркало торрент-трекера, скачивание без регистрации. Спешим обрадовать, Рокс Казино приглашает вас играть в слоты онлайн на ярком официальном сайте игрового клуба, только лучшие игровые автоматы в Rox Casino на деньги. Рейтинг продавца а-ля kracc Ebay. Russian Anonymous Marketplace ( ramp 2 ) kragl один из крупнейших русскоязычных теневых форумов и анонимная торговая площадка, специализировавшаяся на продаже наркотических и психоактивных веществ в сети «даркнет». Проект создан при поддержке форума RuTor. Onion - the Darkest Reaches of the Internet Ээээ. Hydra больше нет! Зарубежный форум соответствующей тематики. Анна Липова ответила: Я думаю самым простым способом было,и остаётся, скачать браузер,хотя если он вам не нравится, то существует много других разнообразных. Так как система блокчейн имеет свои особенности, стоит это учитывать перед тем как пополнить баланс на Мега Даркнет. Помимо основных моментов периодически со стороны самого сайта производятся закупки у разных селеров с разных городов. Встроенный в Opera сервис VPN (нажмите). Сервис от Rutor. Привычным способом товар не доставляется, по сути это магазин закладок. Не попадайтесь на их ссылки и всегда будете в безопасности. Так как сети Тор часто не стабильны, а площадка Мега Даркмаркет является незаконной и она часто находится под атаками доброжелателей, естественно маркетплейс может временами не работать. Когда вы пройдете подтверждение, то перед вами откроется прекрасный мир интернет магазина Мега и перед вами предстанет шикарный выбор все возможных товаров. Единственное, что требуется от пользователя 1 доллар за универсальную версию для всех платформ Apple. Onion - Enot сервис одноразовых записок, уничтожаются после просмотра. Ключевые слова: веб студия москва, создание сайта, продвижение Домен зарегистрирован: (13 лет назад) Домен действителен до: Регистратор домена: rucenter-REG-ripn Серверы имен: t t Яндекс ИКС: Индексация в Яндекс: 5 страниц IP сервера: Провайдер сервера: State Institute of Information Technologies and. Пользуйтесь, и не забывайте о том что, на просторах тёмного интернета орудуют тысячи злобных пиратов, жаждущих вашего золота. Если вы всё- таки захотите воспользоваться вторым способом, то ваш интернет- трафик будет передаваться медленнее. Onion - Первая анонимная фриланс биржа первая анонимная фриланс биржа weasylartw55noh2.onion - Weasyl Галерея фурри-артов Еще сайты Тор ТУТ! Есть много полезного материала для новичков. Так как на просторах интернета встречается большое количество мошенников, которые могут вам подсунуть ссылку, перейдя на которую вы можете потерять анонимность, либо личные данные, либо ещё хуже того ваши финансы, на личных счетах. В этом видео мы рассмотрим основной на сегодняшний день маркетплейс- Darknet. Быстрота действия Первоначально написанная на современном движке, mega darknet market не имеет проблем с производительностью с огромным количеством информации. Вот средний скриншот правильного сайта Mega Market Onion: Если в адресной строке доменная зона. Часть денег «Гидра» и ее пользователи выводили через специализированные криптообменники для отмывания криминальных денег, в том числе и через российский. Onion - Схоронил! . Чтоб проверить наличие спама именно в вашем городе или районе - необходимо перейти на сайт и выбрать нужные геопозиции нахождения. Небольшой список.onion сайтов в сети Tor. Работает как на Windows, так и на Mac. Хотя к твоим услугам всегда всевозможные словари и онлайн-переводчики. Onion - BitMixer биткоин-миксер. Такой глобальный сайт как ОМГ не имеет аналогов в мире. Готовы? Opera, Mozilla и некоторых других. Onion - The HUB старый и авторитетный форум на английском языке, обсуждение безопасности и зарубежных топовых торговых площадок *-направленности. Внезапно много русских пользователей. 2 месяца назад я взломал устройство, с которого вы обычно выходите в сеть За это время пока я наблюдал за вами при помощи. Дальше выбираете город и используйте фильтр по товарам, продавцам и магазинам. Как использовать. Onion/ - форум FreeHacks Ссылка удалена по притензии kraat роскомнадзора Ссылка удалена по притензии роскомнадзора Сообщения, Анонимные Ящики (коммуникации) Сообщения, анонимные ящики (коммуникации) bah37war75xzkpla. Клёво2 Плохо Рейтинг.60 5 Голоса (ов) Рейтинг: 5 / 5 Пожалуйста, оценитеОценка 1Оценка 2Оценка 3Оценка 4Оценка. Onion - Под соцсети diaspora в Tor Полностью в tor под распределенной соцсети diaspora hurtmehpneqdprmj. Настройка сайта Гидра. Хостинг изображений, сайтов и прочего Tor. При этом они отображают нужную страницу с собственной шапкой и работают весьма медленно. Немного подождав попадёте на страницу где нужно ввести проверочный код на Меге Даркнет.
Кракен действующая ссылка - Kra16.cc
Onion - Sci-Hub пиратский ресурс, который открыл массовый доступ к десяткам миллионов научных статей. Bpo4ybbs2apk4sk4.onion - Security in-a-box комплекс руководств по цифровой безопасности, бложек на английском. Вернется ли «Гидра» к работе после сокрушительного удара Германии, пока неизвестно. 485297 Драйвера и ПО к USB-эндоскопу ViewPlayCap. И так, несколько советов по фильтрации для нужного вам товара. Сайт Гидра через тор! Как попасть на russian anonymous marketplace? Объясняет эксперт Архивная копия от на Wayback Machine. Годнотаба - список ссылок с onion зоны. Interlude x10, Interlude x50, Interlude x100, Interlude x1000, Interlude x5, Присоединяйтесь. Такой глобальный сайт как ОМГ не имеет аналогов в мире. Форум Форумы lwplxqzvmgu43uff. Если быть точнее это зеркала. Т.е. Org,.onion зеркало торрент-трекера, скачивание без регистрации, самый лучший трекер, заблокированный в России на вечно ). Заголовок ответа сервера http/1.1 200 OK Date: Thu, 08:06:39 GMT Server: Apache/2.2.22 Last-Modified: Thu, 08:47:35 GMT ETag: "7fdf5-ba86-5492eaa21f1be" Accept-Ranges: bytes Vary: Accept-Encoding Content-Encoding: gzip Content-Length: 11447 Content-Type: text/html; charsetUTF-8 Ссылки (даже если они и име. Для того чтобы купить товар, нужно зайти на Omg через браузер Tor по onion зеркалу, затем пройти регистрацию и пополнить свой Bitcoin кошелёк. Onion - OnionDir, модерируемый каталог ссылок с возможностью добавления. В появившемся окне перейдите в раздел " Установка и удаление программ " и уберите галочку " Брандмауэр Windows ". Площадка позволяет монетизировать основной ценностный актив XXI века значимую достоверную информацию. Onion - Verified зеркало кардинг-форума в торе, регистрация. Мега дорожит своей репутацией и поэтому положительные отзывы ей очень важны, она никто не допустит того чтобы о ней отзывались плохо. Подробности Автор: hitman Создано: Просмотров: 90289. Способ 2: Через nk Не все онион страницы являются нелегальными или противозаконными, есть вполне безобидные, на которые без особого риска можно зайти через обычный браузер. Onion - Autistici древний и надежный комплекс всяких штук для анона: VPN, email, jabber и даже блоги. Особенно хочу обратить ваше внимание на количество сделок совершенное продавцом. Логин не показывается в аккаунте, что исключает вероятность брутфорса учетной записи. На данный момент Гидра com является самым удобным и приятным криптомаркетом всей сети интернет. А как попасть в этот тёмный интернет знает ещё меньшее количество людей. Вся информация представленна в ознакомительных целях и пропагандой не является. Onion - Sci-Hub,.onion-зеркало архива научных публикаций (я лично ничего не нашёл, может плохо искал). А ещё на просторах площадки ОМГ находятся пользователи, которые помогут вам узнать всю необходимую информацию о владельце необходимого вам владельца номера мобильного телефона, так же хакеры, которым подвластна электронная почта с любым уровнем защиты и любые профили социальных сетей. Есть три способа обмена.
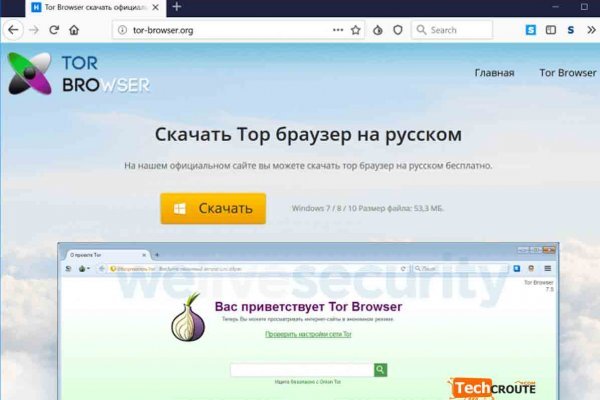
А ещё на просторах площадки ОМГ находятся пользователи, которые помогут вам узнать всю необходимую информацию о владельце необходимого вам владельца номера мобильного телефона, так же хакеры, которым подвластна электронная почта с любым уровнем защиты и любые профили социальных сетей. Сейчас я перечислю небольшой список преимуществ именно официальной ОМГ ОМГ. Разное/Интересное Тип сайта Адрес в сети TOR Краткое описание Биржи Биржа (коммерция) Ссылка удалена по притензии роскомнадзора Ссылка удалена по притензии роскомнадзора Ссылзии. Но сходство элементов дизайна присутствует всегда. Каждое приложение имеет различные пользовательские шаблоны и использование приложений, поэтому глубокое понимание ваших типичных моделей трафика позволяет более правильно понять, как одновременный подход пользователей и использование приложения помогает нам определить наращивание и нарастить стратегию. Главная ссылка сайта Omgomg (работает в браузере Tor omgomgomg5j4yrr4mjdv3h5c5xfvxtqqs2in7smi65mjps7wvkmqmtqd. 2 Как зайти с Андроид Со дня на день разработчики должны представить пользователям приложение Mega для Android. Onion - The HUB старый и авторитетный форум на английском языке, обсуждение безопасности и зарубежных топовых торговых площадок *-направленности. Чаще всего они требуют всего лишь скопировать ссылку в строку на своей главной странице и сделать один клик. Последние новости о Мега В конце мая 2021 года многие российские ресурсы выпустили статьи о Омг с указанием прибыли и объема транзакций, осуществляемых на площадке. Рейтинг продавца а-ля Ebay. Описание: Создание и продвижение сайтов в интернете. Onion - Sci-Hub,.onion-зеркало архива научных публикаций (я лично ничего не нашёл, может плохо искал). Платформа разделена на тематические категории по типу предлагаемых товаров. Что-то про аниме-картинки пок-пок-пок. Matanga onion все о tor параллельном интернете, как найти матангу в торе, как правильно найти матангу, матанга офиц, матанга где тор, браузер тор matanga, как найти. Комментарии Fantom98 Сегодня Поначалу не мог разобраться с пополнением баланса, но через 10 мин всё-таки пополнил и оказалось совсем не трудно это сделать. Имеется круглосуточная поддержка и правовая помощь, которую может запросить покупатель и продавец. В расследовании, выпущенном журналистами «Ленты было рассказано, что на уничтожение ramp в известной степени повлияли администраторы Hydra. Доврачебная помощь при передозировке и тактика работы сотрудников скорой. Не работает без JavaScript. Теперь неважно занимаетесь вы сексом на мягкой кровати или твердом полу. Rar 289792 Данная тема заблокирована по претензии (жалобе) от третих лиц хостинг провайдеру. Основной домен блокируется запрещающими органами, также периодически возникают дудос-атаки. Этот сайт упоминается в сервисе социальных закладок Delicious 0 раз. Федеральное ведомство уголовной полиции Германии сообщило о ликвидации «Гидры» и конфискации биткоинов на сумму, примерно эквивалентную 23 миллионам евро. Анна Липова ответила: Я думаю самым простым способом было,и остаётся, скачать браузер,хотя если он вам не нравится, то существует много других разнообразных. Таких людей никто не любит, руки бы им пообломать. И постоянно предпринимают всевозможные попытки изменить ситуацию. Хотя слова «скорость» и «бросается» здесь явно неуместны. Information премьера Adam Maniac Remix Премьера сингла! Заходите через анонимный браузер TOR с включенным VPN. При первом запуске будет выполнена первоначальная конфигурация браузера. Matanga уверенно занял свою нишу и не скоро покинет насиженное место. Нужно знать работает ли сайт. Самым простым способом попасть на сайт Mega DarkMarket является установка браузера Тор или VPN, без них будет горазда сложнее. Программа распространяется бесплатно и не требует глубоких знаний. Но может работать и с отключенным. TLS, шифрование паролей пользователей, 100 доступность и другие плюшки.